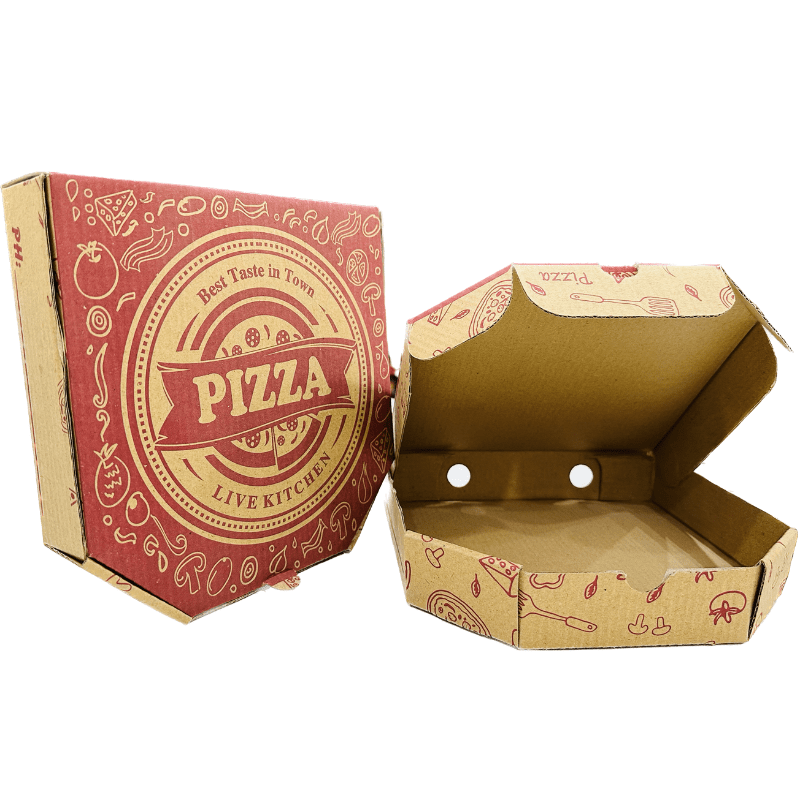
The Evolution of the Pizza Box: From Clay Pots to Eco-Friendly Solutions
Introduction
When we think of pizza, our minds often conjure up images of gooey cheese, flavorful toppings, and a perfectly crispy crust. While these elements undoubtedly play a crucial role in the pizza experience, there’s another unsung hero that deserves its moment in the spotlight—the humble pizza box. The pizza box is much more than a cardboard container; it’s a testament to the ingenuity of human design, a symbol of convenience, and a silent companion on countless pizza nights. In this article, we’ll explore the history, evolution, and fascinating facts surrounding the pizza box.
History Of Pizza Box
The concept of packaging for food delivery is not new. In ancient Rome and Greece, people used clay pots to transport cooked foods. However, it wasn’t until the 19th century that the idea of the pizza box, as we know it today, began to take shape. The development of corrugated cardboard and the rise of the pizza industry in the United States played pivotal roles in its evolution.
The First Pizza Delivery
The concept of delivering pizza to homes began in the early 20th century. One of the pioneers of pizza delivery was the famous Lombardi’s Pizzeria in New York City. In 1905, they became the first pizzeria to offer pizza delivery services, using simple paper wrappings to transport their pizzas.
The Birth of the Modern Pizza Box
The classic pizza box, with its distinctive square shape, was patented by Ermanno and Louis Tozzoli in 1963. This innovative design allowed for easy stacking and efficient storage, making it ideal for pizza delivery. Over the years, the pizza box has undergone various improvements, including features like heat-retaining layers, vents to prevent sogginess, and even built-in plates for convenient dining.
Pizza Boxes Go Green
In recent years, there has been a growing emphasis on environmental sustainability. As a result, many pizza companies have transitioned to eco-friendly pizza boxes made from recycled materials and designed for easy recycling. These initiatives aim to reduce the environmental impact of the pizza industry.
Fun Facts About Pizza Boxes
- The World’s Largest Pizza Box: In 2012, a team in Italy created the world’s largest pizza box, measuring over 13 feet in length and 6.5 feet in width. This giant box housed a massive pizza that set a world record.
- Pizza Box Art: Some pizza boxes are adorned with creative and colorful artwork. Pizza chains often hold contests for artists to design limited-edition pizza boxes.
- Pizza Box Technology: There have been experiments with incorporating technology into pizza boxes. For instance, some boxes come with built-in QR codes that can be scanned for discounts or interactive games.
- Pizza Box Folding World Record: In 2015, Scott Wiener set a Guinness World Record for the fastest time to fold 10 pizza boxes. He accomplished this feat in just 46.6 seconds!
Conclusion
The pizza box, a seemingly ordinary item, has played an integral role in the world of pizza delivery, ensuring that our beloved pies arrive at our doorstep hot, fresh, and intact. Its history is a testament to innovation, convenience, and the enduring love for this iconic dish. So, the next time you enjoy a delicious slice of pizza, take a moment to appreciate the unassuming pizza box that made it all possible. It’s not just a container; it’s a symbol of culinary delight and the joy of sharing a meal with loved ones.
To get customize quality pizza box you may contact us here
Thank you